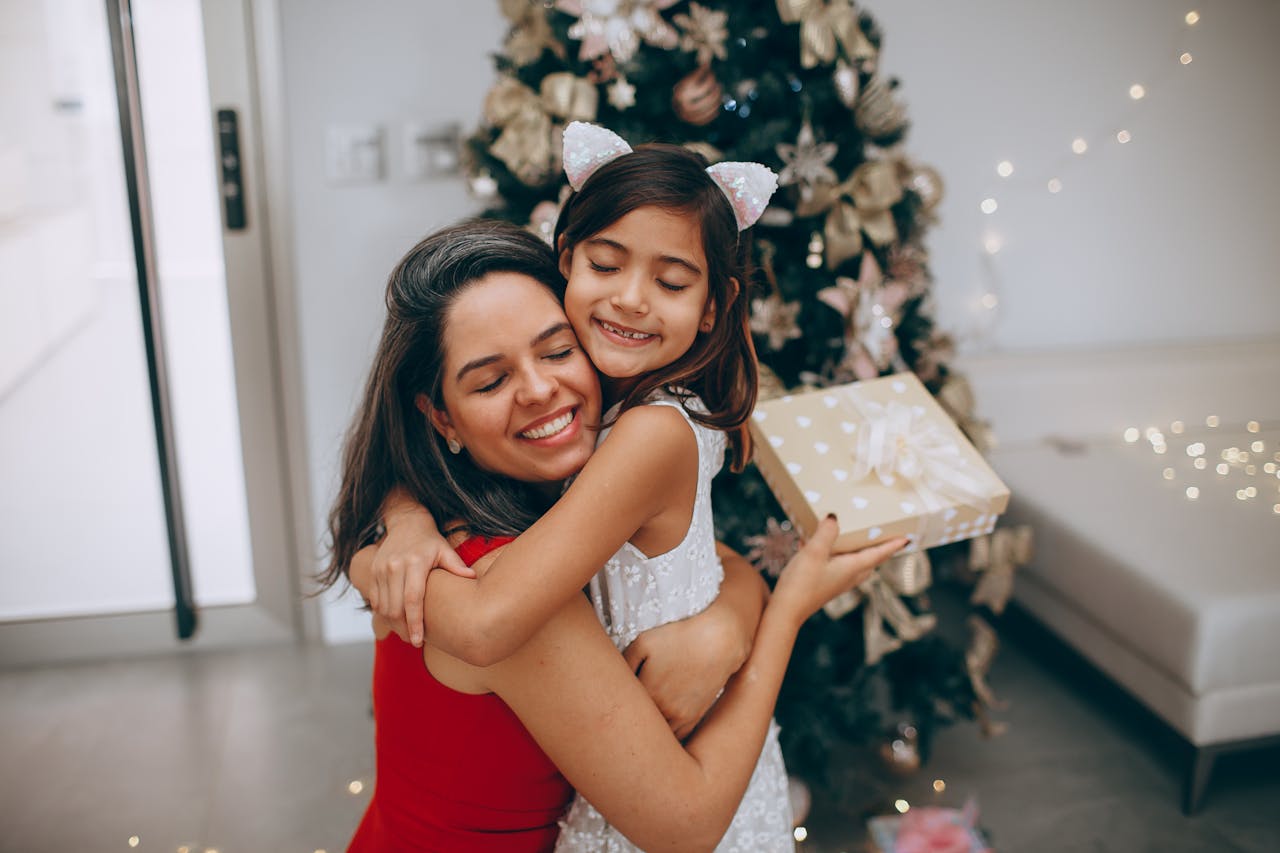
From Basics to Brilliance: A Beginner's Guide to Injection Molding
Injection molding, a groundbreaking manufacturing technique with history, has been utilized for years to craft top-notch plastic components.
Whether it involves parts for the sector or the production of various items like kitchen tools and medical equipment, injection molding stands out as a cost-efficient and effective method to materialize innovative concepts.
In this manual on injection molding, we aim to guide you through the fundamentals of this process, covering everything from its principles to its advantages and constraints. Whether you're a student delving into manufacturing techniques or an entrepreneur seeking to revamp your product range, this guide promises to lay the groundwork in the realm of injection molding.
Understanding Injection Molding
Before we move further in this beginner’s guide to Injection Molding, let’s try to understand what Injection Molding is.
Injection molding entails injecting plastic into a tailor-made mold under intense pressure. Post-cooling, the mold is opened up, allowing for the ejection of the part. This method facilitates large-scale production of items within a short timeframe.
The Cycle
The injection molding cycle encompasses phases that ensure accuracy and consistent outcomes. These stages include;
1. Clamping:
The two mold halves are firmly secured together using force to prevent any plastic seepage during processes.
2. Injection Molding Process Steps
Material Injection
The molten plastic is pushed into the mold under pressure, taking on the shape of the mold.
Cooling Phase
The plastic cools and solidifies inside the mold, and cooling channels within the mold can help speed up this process.
Mold Opening
Once the plastic has cooled completely, the mold is opened up.
Ejection Stage
After opening the mold, pins or ejectors are used to push out the parts for inspection and removal.
Benefits of Injection Molding
Injection molding provides advantages compared to manufacturing techniques;
1. Efficiency:
Injection molding stands out for its ability to produce tens or hundreds of thousands of units quickly.
2. Cost Effectiveness
While initial setup costs may be per unit, expenses decrease significantly as production volume increases, making it ideal for production.
3. Design Flexibility
With injection molding, intricate and detailed parts can be produced accurately, offering a range of options that can mimic different textures and finishes.
4. Material Variety
Injection molding allows for the use of a range of thermoplastics, like ABS plastic, polycarbonate, and nylon, each possessing its distinct characteristics.
5. Consistent Precision
Injection molding excels in achieving levels of accuracy and consistency, producing parts that adhere to standards with minimal variation.
Challenges of Injection Molding
Despite its advantages, injection molding does have some limitations:
1. Investment
Creating molds involves upfront expenses. However, these costs can be offset over time. When manufacturing quantities of parts, it is crucial to assess the investment against projected demand for cost-effectiveness.
2. Design Limitations
Certain designs may pose difficulties for injection molding due to factors like walls or complex internal features.
3. Time Constraints
The production process, including mold design and testing, may span weeks or even months before production commences.
4. Impact
While progress is being made in recycling within the plastics industry, sustainability issues persist regarding waste and disposal linked to injection molding.
Choosing the Right Injection Molding Partner
Once you have a grasp of the basics and understand the advantages and limitations of injection molding, the next crucial step is selecting the right injection molding partner. The success of your project hinges on finding a reliable, experienced, and capable manufacturer who can bring your ideas to life. Here are some factors to consider when choosing an injection molding partner:
1. Expertise and Experience
Look for a manufacturer with extensive experience in injection molding, especially in your particular industry or niche. They should have a deep understanding of material properties, mold design, and production processes.
2. Technology and Capabilities
Assess their equipment, machinery capabilities, and technological advancements. A reputable manufacturer will invest in state-of-the-art machinery to ensure consistent quality and efficiency.
3. Quality Assurance
Ensure that the prospective partner has established quality control measures throughout every stage of the manufacturing process. Ask for certifications such as ISO 9001 to ensure adherence to international standards.
Wrapping Up
From components to household products and appliances, injection molding has emerged as a technique in contemporary manufacturing practices.
The capacity to manufacture top-notch plastic components swiftly and effectively has brought about a transformation in sectors across the globe.
Although this introductory manual only delves into the aspects of injection molding, we believe it has provided you with insights into its pros and cons. Equipped with this information, you can delve deeper. Unlock the possibilities offered by injection molding technology.
Trending
-
1 Jocko Willink's Inspirational Life & Net Worth
Aaqil Ashraf -
2 How Art Shapes Culture and Reflects Human Experience
Luke Fitzpatrick -
3 Meet Felix Williams and Maria Arthuer: The Parents of World Class Winger Nico Williams
Felix Yim -
4 Kai Cenat's Dad and the Enduring Public Interest
Aaqil Ashraf -
5 London Tube Stations Closed as Workers Stage Strikes
Mihir Gadhvi
Comments